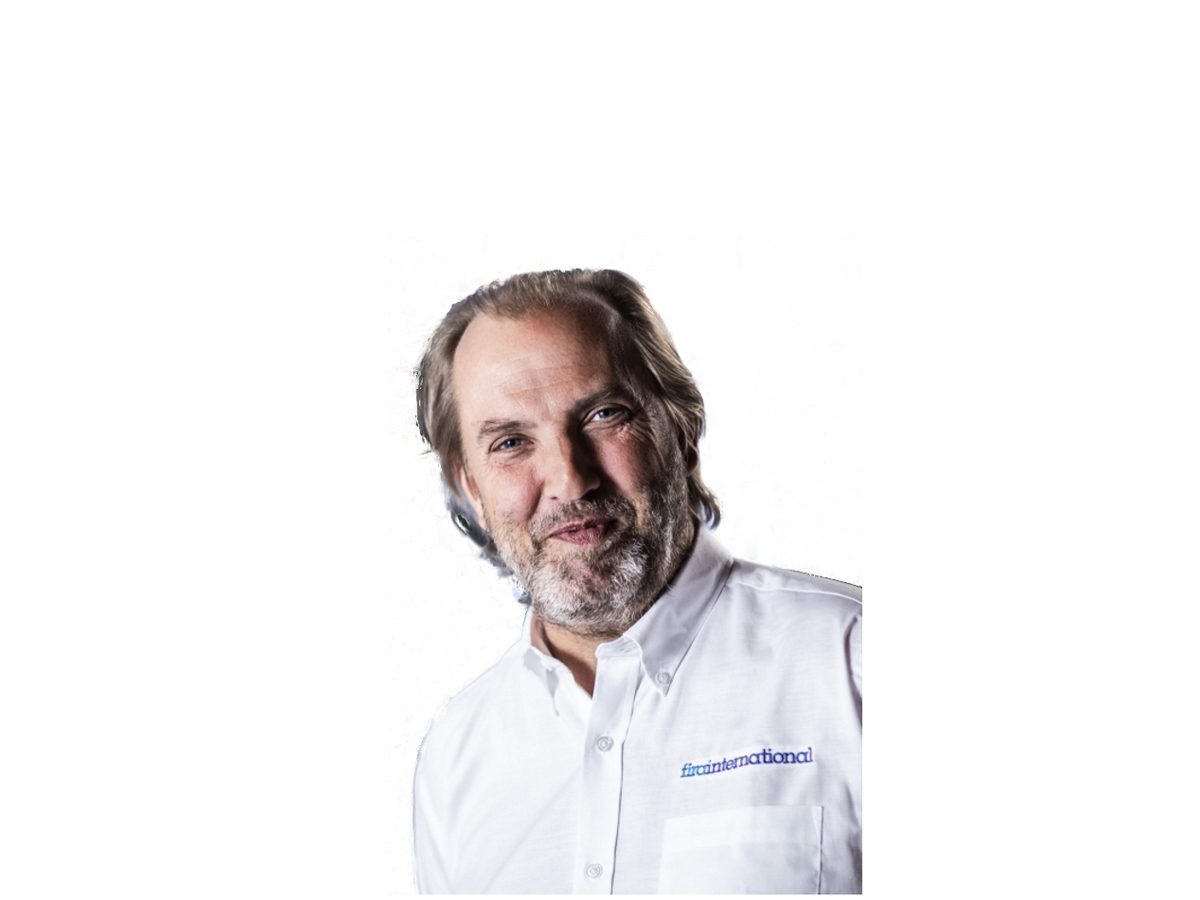
Testing times for furniture retailers
Five months into 2023 and nine different items of furniture have been recalled by the Government, with all bar one product failing to comply with the Furniture and Fire Safety Regulations 1988. This represents a fifty percent increase on 2022 levels with more than half of the year to go, and a two hundred per cent increase on 2021. Here, Howard James, Testing and Technical Manager at FIRA International, looks at what may be causing the issues, and what retailers must look out for when bringing new furniture products to market.
It's impossible to ignore the significant increase in flammability-related product recalls for upholstered furniture that has occurred over the past 18 months.
First and foremost, it’s important to remember the purpose of product recalls. They are not undertaken lightly and only occur when a product has failed compliance testing to the relevant regulations and standards and therefore could represent a genuine safety risk to the general public.
When a product fails, it is because one or more specific materials used within its construction have been found to be non-compliant. For upholstered furniture, the most common material failures are the fabric or the foam.
Non-compliant furniture – who is liable?
One conceivable reason for the greater number of product recalls in recent years is an increase in spot testing from Trading Standards. What these spot tests can reveal is a potential discrepancy between the materials used for flammability testing by the manufacturer, and those that are actually used when the product goes into mass production.
Therefore, it is vitally important that retailers pay particular attention to the flammability test reports during their due diligence.. If there is no traceability for the material used during flammability testing, such as a batch number or reference code, then it can be very difficult to cross reference that sample with the final material used when the unit goes into production.
When it comes to ultimate liability for a non-compliant item, if it is imported then it is the importer’s responsibility to ensure the materials used are compliant with the flammability regulations of that country. However, as the retailer is the one that is placing the product on the market, they are the ones who will face reputational damage should the product be found to be non-compliant.
Protect your reputation – spot testing and third-party certification
What, therefore, should retailers do to protect their hard-earned reputation and ensure their products remain fully compliant with UK flammability regulations?
First and foremost, we’d recommend independently spot-testing products once they have been imported, prior to putting them on the market.
The cost of sacrificing one unit to be taken apart and submitted for various flammability tests will pale in comparison to the costs incurred of recalling that entire product range. Regular spot testing is also recommended if there have been any significant changes to the supply chain prior to importation, too.
Another way to safeguard against product recalls is to use a recognised third-party to regularly audit your supply chain to ensure the accuracy and authenticity of all test reports for the individual materials used and the traceability to the final product supplied. The Furniture Industry Research Association’s ‘Compliance Scheme for the Fire Performance of Upholstered Furniture’ involves regular auditing and re-testing to ensure retailers, manufacturers and end-users can be confident that the materials used will be compliant with the required standards and regulations. The scheme also incorporates a Primary Authority Co-ordinated Partnership with Hertfordshire Trading Standards. This means that Certified Companies, as participants of the scheme, will be part of a regulated group and benefit from Assured Advice from Trading Standards.
Ultimately, the number of product recalls issued to furniture retailers is showing no sign of slowing down. Proactive flammability testing and supply chain audits are two proven ways of ensuring your products remain compliant and your brand reputation remains intact.
You can find out about FIRA’s flammability testing for upholstered furniture here.